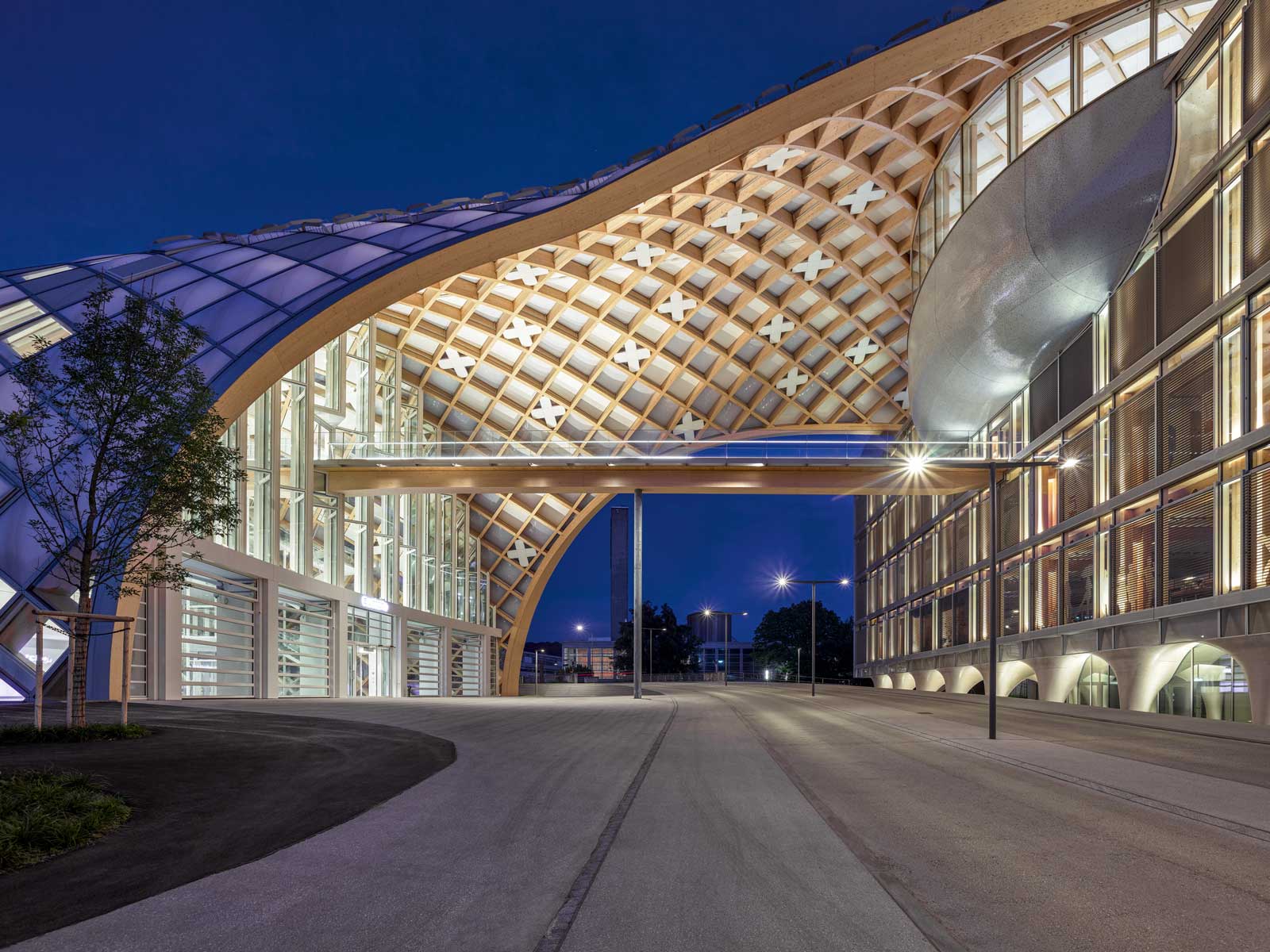
„Es geht um den Respekt vor dem Material.“
Kai Strehlke (Blumer-Lehmann AG) im Gespräch mit Urs Hirschberg (GAM)Der Architekt Kai Strehlke leitet seit fünf Jahren die digitalen Prozesse in der CAD/CAM-Produktion der Schweizer Holzbaufirma Blumer-Lehmann. Davor war er zehn Jahre als Head IT beim Architekturbüro Herzog & de Meuron tätig. Bei Herzog & de Meuron hat er an vielen international bekannten Projekten des Büros mitgearbeitet. Er kennt also die Architekturpraxis nicht nur aus dem speziellen Blickwinkel des Holzbaus, auf den er sich inzwischen spezialisiert hat. Blumer-Lehmann ist ein traditionsreiches ostschweizerisches Familienunternehmen. Der Erlenhof, wo 1875 das erste Sägewerk gegründet wurde und bis heute mit dem zweiten Standort im Ort die gesamte Produktion stattfindet, liegt idyllisch gelegen bei Gossau (Abb. 2). Für zeitgenössische Holzarchitektur, insbesondere im Bereich Freiformgeometrien, ist Blumer Lehmann eine international profilierte erste Adresse. In jüngster Vergangenheit hat Kai Strehlke unter anderem am neuen Swatch Hauptgebäude (Architektur: Shigeru Ban Architects, Paris/Tokio) und an der Moschee in Cambridge (Architektur: Marks Barfield Architects, London) maßgeblich mitgearbeitet. Die meisten Abbildungen im Beitrag stammen von diesen beiden Projekten. Das Gespräch mit Kai Strehlke, der vor seinem Engagement bei Blumer-Lehmann im Jahr 2015 ein Semester lang als Gastprofessor an der TU Graz unterrichtete, fand im September 2020 per Videokonferenz statt.
GAM: Du arbeitest jetzt seit fünf Jahren bei Blumer Lehmann, einem Familienbetrieb. Angesichts deiner langen Zeit bei einem der weltweit führenden Architekturbüros wundert man sich vielleicht, dass du bei einer Holzbaufirma im ländlichen Raum gelandet bist. Aber bei Blumer Lehmann kannst du ebenfalls an äußerst spannenden Projekten arbeiten, die nachher weltweit umgesetzt werden. Der Firma gelingt das Kunststück, als produzierender Betrieb im Hochlohnland Schweiz international kompetitiv zu sein. Ihr fertigt Bauteile in der teuren Schweiz und verfrachtet sie nach England, sogar ins Holzland Norwegen, ja sogar ins weit entfernt gelegene und für deutlich niedrigere Lohnkosten bekannte Korea. Wie geht das? Was macht Blumer Lehmann so viel besser als die Konkurrenten vor Ort?
KS: Die Firma hat eine lange Tradition. Sie wurde 1875 als Sägerei gegründet. Wir haben eine lange Holzbautradition und verfügen über ein enormes Wissen über den Werkstoff Holz. Im Unternehmen legen wir großen Wert auf die Ausbildung von Fachkräften und bilden Lernende aber auch Studenten aus Fachhochschulen aus. Gleichzeitig sind wir unglaublich daran interessiert, was Holz heute und in der Zukunft für Potentiale bietet. Außerdem sind wir sehr gut mit Universitäten wie Stuttgart, der EPFL Lausanne, der ETH Zürich und mit der EMPA (Eidgenössische Materialprüfungs- und Forschungsanstalt) vernetzt. Wir haben viele Projekte, bei denen man verstehen lernt, was man mit Holzfasern auch in Zukunft machen kann. Der Blick einerseits in die Vergangenheit aber auch das Offensein für die Zukunft, das zeichnet die Firma aus. Aber nochmals zu deiner Frage. Im Ausland sind wir vor allem mit unseren Freiformen wettbewerbsfähig, da wir dort über einen Know-how-Vorsprung zu unseren Mitbewerbern verfügen. Unser Hauptmarkt ist aber nach wie vor die Schweiz.
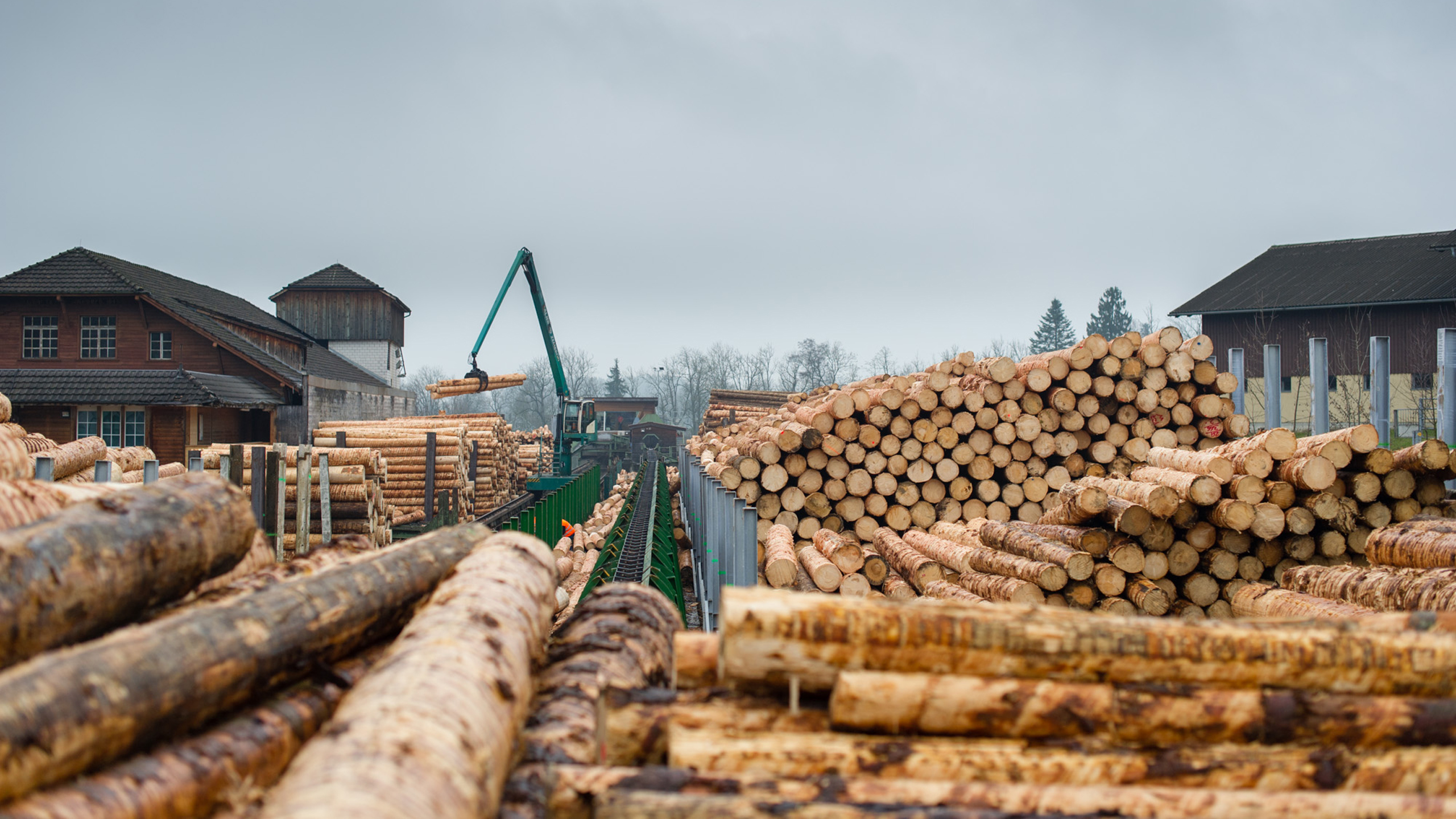
GAM: Du erwähnst den Forschungskonnex. Ist der das Geheimnis? In vielen Branchen ist die Produktion ja schon lange nach China abgewandert. Gelingt es euch, die Schweizer Personalkosten in der Produktion durch besseres Know-how im Engineering wettzumachen?
KS: Die Forschungswidmung ist wichtig. Es ist wichtig, sich mit potenten Forschungspartnern zu vernetzen und auch im Haus selbst Forschung zu betreiben. Die Projekte, die wir ins Ausland verkaufen sind meist Leuchtturmprojekte. Andere Firmen sind oft gar nicht in der Lage, diese zu bauen. Da gibt es nur wenige, die das können. Blumer Lehmann hat dafür die Kompetenz, nicht unbedingt, weil wir extreme SpezialistInnen haben, sondern weil wir intern als Team sehr gut aufgestellt sind und über viel Fachwissen verfügen: Zimmerleute, StatikerInnen, Holzbau-IngenieurInnen, Leute, die in der Lage sind, die komplexe Logistik zu bewältigen und auch Leute wie ich, die mit den digitalen Prozessen sehr gut klarkommen, damit solche komplexen Entwürfe auch gefertigt werden können. Das, was uns ausmacht, ist das Team.
Ein weiterer Grund, warum wir erfolgreich sind, ist Katharina Lehmann, unsere CEO, sie ist mutig, unternehmerische Schritte zu gehen, wobei diese oft mit relativ viel Risiko verbunden sind. Sie nimmt Projekte an, bei denen man eventuell am Anfang noch nicht weiß, wie man sie fertigen wird. Aber sie hat das Vertrauen in ihr Team, das in der Lage sein wird, Lösungen zu finden. Das ist das, was uns als Firma auszeichnet.
Diese internationalen Projekte könnte man auch kritisch sehen. Es ist nicht besonders nachhaltig, in der Schweiz das Holz zu fertigen und mit Lkws nach England oder mit Schiffen nach Korea zu transportieren, um sie dort aufzubauen. Aber ich glaube, dass diese Projekte, diese Leuchtturmprojekte, dem Holzbau generell einen unglaublich guten Dienst leisten. Sie treiben den Holzbau auch in anderen Ländern voran. Gerade England ist ein sehr backsteinlastiges Land. Dort hat ein Projekt wie die Moschee in Cambridge eine Signalwirkung. Auch in der Schweiz hat der Holzbau erst in der letzten Zeit, gerade im Wohnungsbau, wieder an Bedeutung gewonnen. Diese Leuchtturmprojekte helfen dem Material, wieder mehr Aufschwung zu bekommen.
GAM: Diese Leuchtturmprojekte haben viel mit der digitalen Fabrikation zu tun, auf die du dich spezialisiert hast. In Bezug auf Digitalisierung und Robotisierung des Bauwesens passiert ja derzeit sehr viel. Andererseits ist Holz als nachhaltiger Baustoff stark im Trend. Als Firma profitiert ihr sicher davon, dass Holzverarbeitung und Digitalisierung so gut zusammenpassen. Es gibt im Holzbau ein hohes Potenzial für die Vorfertigung. Man kann damit Bauprozesse beschleunigen. Wie beobachtest du die allgemeine Entwicklung in Richtung Holzbau, sowohl in Bezug auf die Digitalisierung aber auch im Zusammenhang mit dem Nachhaltigkeitsthema?
KS: Du sprichst zwei Themen an: Nachhaltigkeit und Digitalisierung. Die Nachhaltigkeit ist ein hochaktuelles Thema, vor allem, wenn man sich Bewegungen wie Fridays for Future anschaut und die allgemeine CO2-Debatte, die gerade sehr stark in der Politik behandelt wird, oder nach Corona wieder behandelt werden wird. Holz ist ein Material, das in dieser Debatte eine wichtige Rolle spielt. Holz bindet CO2, Beton verbraucht CO2. Holz kann eine Antwort liefern auf die Diskussion der Nachhaltigkeit im Bauwesen. Das Bauwesen ist bekanntlich für 35 bis 40 Prozent des CO2-Ausstoßes verantwortlich. Dass Holz in Bezug auf die CO2-Bilanz so ein sinnvolles Material ist, hilft natürlich dem Holzbau.
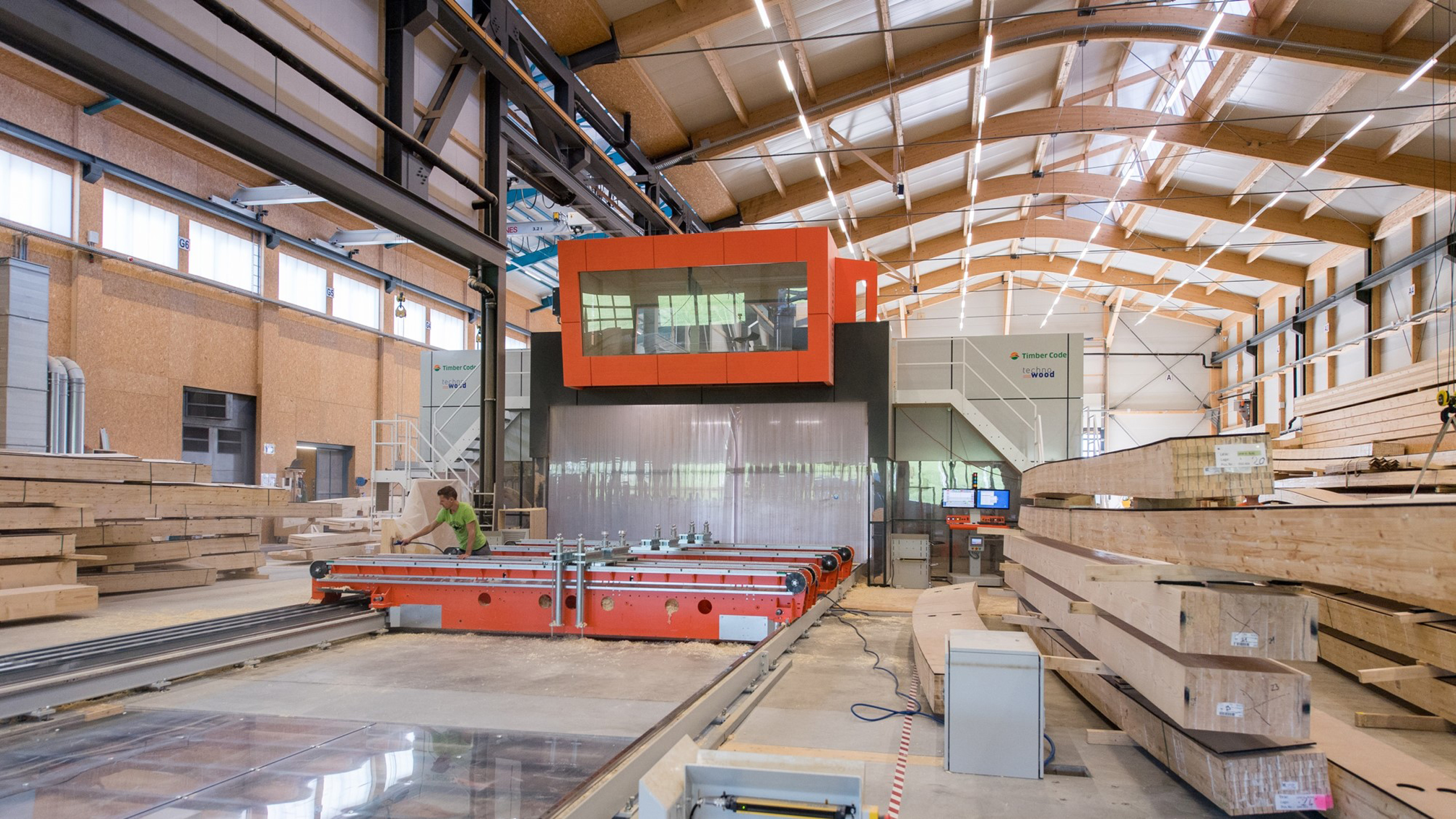
Bei der Digitalisierung gibt es zwei große Tendenzen: die Vorfabrikation und das Bauen in situ, also das Bauen auf der Baustelle. Beton gibt es auch in der Vorfabrikation, aber viel Beton oder Stein wird vor Ort verbaut. Beim Holz hat die Vorfabrikation eine lange Tradition. Schon die deutschen Fachwerkhäuser wurden auf Plätzen vor den Dörfern abgebunden. Es gab eine Logistiklösung, um die Teile nachher in die Dörfer zu bringen und dort wieder zusammenzubauen. Das sind Erfindungen, die schon vor hunderten Jahren gemacht worden sind, die schon immer dem Holz einen Vorteil gegeben haben in der Vorfabrikation. Die Digitalisierung ist nur die logische Weiterentwicklung dieser Praktiken mit den heutigen technischen Möglichkeiten. Holz hat hier große Vorteile. Dass man sich eine Zeit lang vom Holz abgewendet hat, hatte vor allem damit zu tun, dass Holz brennen kann. Viele Dörfer und Städte sind wegen Bränden in Holzhäusern fast oder gänzlich vernichtet worden. Den Brandschutz haben wir heute im Griff. Das heißt, es macht heute wieder Sinn, das Holz in die Städte hinein zu bringen.
Für Baustellen in der Stadt ist die Vorfabrikation ein enormer Vorteil: Man ist in der Lage, vor der Stadt hochkomplexe Teile vorzufertigen, die dann in der Stadt legomäßig zusammengebaut werden können. Man hat kurze Bauzeiten, kleine Baustellen. Holz ist perfekt für die Vorfabrikation geeignet. Es ist auch nicht so schwer wie Stein oder Beton. Die Städte wachsen, wir brauchen immer mehr Wohnraum. Wir können nicht nur neu bauen, mit einem leichten Material wie Holz können wir auch aufstocken und an Gebäude anbauen. Holz ist dafür ein sinnvolles Material. Ich glaube, Holz ist das Material der Zeit.
Was ich im Augenblick erlebe, ist eine Art Pionierhaltung im Holzbau, die ich ähnlich empfinde wie zu den Zeiten von Mies van der Rohe in Berlin oder den USA in den 1920er-Jahren. Ich habe das Gefühl, Holz ist im Augenblick so interessant, wie es damals Glas und Stahl waren. Interessant ist, dass es ein uraltes Material ist, welches wir dabei sind, neu zu entdecken.
GAM: Liegen die Ursachen für diese Neuentdeckung nicht auch in einer anderen Wertschätzung des Materials Holz?
KS: Ich weiß nicht, ob das die Sache zu sehr vereinfacht, aber für mich ist es so: im Zuge der Industrialisierung in den 1950er-, 1960er- und 1970er-Jahren hat man versucht, möglichst standardisiert zu arbeiten. In den Fabriken wollte man deswegen homogene Materialien haben. Die Krönung dieser Entwicklung war, dass man die Faser, die anisotropen Eigenschaften des Holzes, also das, was Holz als Material ausmacht, komplett zerstört hat, indem man es zermahlen und mit Leim wieder zusammengeklebt hat. Das ist eigentlich eine Vergewaltigung des Werkstoffes. Man bekommt dann ein Material, das man „MDF“ nennt, ein homogenes Material, das in alle Richtungen die gleichen Eigenschaften hat. Aber es sind die gleichen schlechten Eigenschaften, denn die Faser, die das Holz so unglaublich kräftig macht, hat man dadurch zerstört. Gerade ist man dabei zu erkennen, dass man besser nicht gegen die Faser, sondern mit der Faser arbeitet.
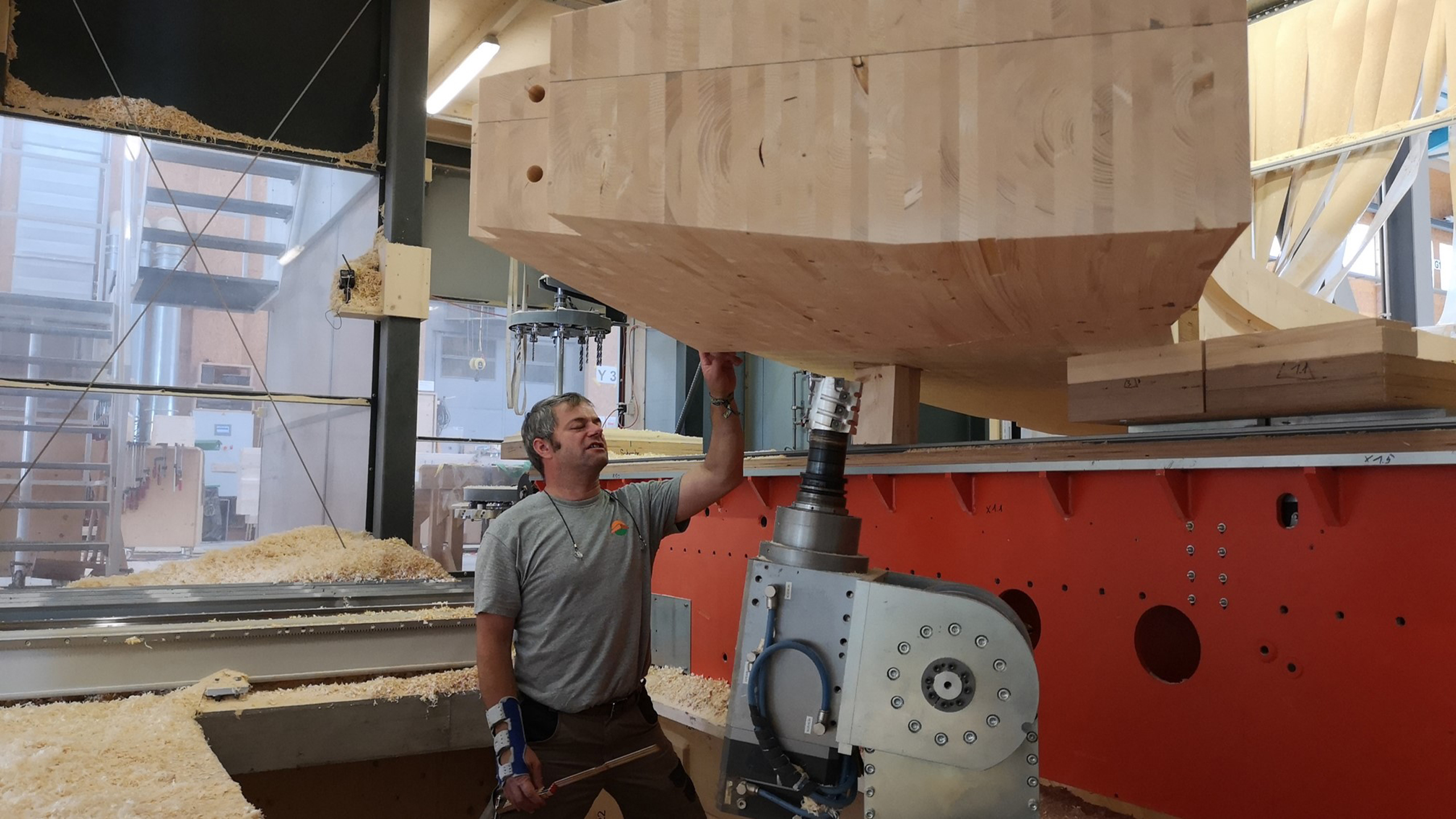
© Blumer-Lehmann AG
GAM: Unser Heftthema ist ja „Rethinking Material“. Du hast gerade dargelegt, dass neu denken auch heißen kann, dass man jene Dinge wieder neu erkennt und zu schätzen lernt, die frühere Generationen schon gewusst haben. Du erwähnst die Nachkriegszeit. Dieses „dumbing down“ des Materials Holz, also diese Faserplatten, die hat man ja auch deswegen gemacht, weil damit alles einfacher wurde. Man musste sich weniger Gedanken machen, man konnte alles einfacher berechnen. Es wird ja alles komplizierter, wenn man den Baustoff so nimmt wie er gewachsen ist, aber man bekommt eben dadurch auch weitere Möglichkeiten. Reden wir jetzt von diesen Möglichkeiten. Bei Blumer Lehmann seid ihr bereit, Neues auszuprobieren und ihr betont auch, dass ihr möglichst früh mit den ArchitektInnen zusammenarbeiten wollt, damit euer Expertenwissen in den Entwurf einfließen kann. Findet das auch statt? Läuft das immer so, dass ArchitektInnen früh auf euch zukommen, wenn sie ein Projekt entwickeln, das auf virtuose Weise mit Holz umgeht?
KS: Ich würde sagen, wenn die hochkomplexen Projekte erfolgreich sind, dann ist es so gelaufen. Es gibt ja die verschiedenen Leistungsphasen, die sind je nach Land etwas unterschiedlich geregelt, aber sowohl in Deutschland als auch in der Schweiz ist es so, dass die ausführenden Unternehmen erst nach der Ausschreibung ins Spiel kommen. Die ArchitektInnen entwickeln das Projekt davor mit FachplanerInnen usw. Die Unternehmen kommen erst danach dazu.
Was wir propagieren und sehr erfolgreich machen, vor allem bei privaten Freiformprojekten, ist, dass wir vor der Ausschreibung einen Piloten, ein Mockup bauen (Abb. 9–10). In diesem Mockup testen wir die Herstellung, die Ästhetik und wir sehen auch, was die Kostentreiber im Projekt sind und wie man diese eventuell reduzieren kann, z.B. indem man Krümmungen reduziert oder leichte Änderungen an der Architektur macht. Es geht nicht darum, die Architektur zu ändern. Es geht darum, die Konsequenzen aus einem Entwurf für die Ausführung aufzuzeigen. Bei privaten Projekten ist das sehr erfolgreich. Bei öffentlichen Ausschreibungen haben wir das Problem, dass wir als Unternehmen erst danach ins Spiel kommen können. Das führt dann oft zu Projekten, die unglaublich schwierig auszuführen sind. Die Projekte werden dann auch wesentlich teurer.
GAM: Das heißt, man müsste eigentlich diese Richtlinien ändern, um das auch bei öffentlichen Ausschreibungen zu ermöglichen. Oder das Mockup müsste schon als Teil der Vorplanungsphase akzeptiert werden und abrechenbar sein. Du sagst, die Richtlinien verhindern ein vernünftiges Vorgehen, das noch dazu Kosten sparen könnte?
KS: Ja!
GAM: Das heißt, ihr seid mit eurem Ansatz eigentlich im Nachteil bei öffentlich ausgeschriebenen Projekten?
KS: Ich glaube nicht, dass wir im Nachteil sind. Oft ist es ja so, dass die Firmen, die billig anbieten, ohne die Konstruktion wirklich auszuloten, sich dann übernehmen. Bei den Blobs, den Freiformarchitekturen, die Ende der 1990er-Jahre aufgekommen sind, konnte man das oft beobachten. Man hat den günstigsten Anbieter genommen, der dann aber nicht in der Lage war, das Projekt umzusetzen. Wenn dann eine Firma pleite gegangen ist, und manchmal ist ja auch noch eine zweite Firma pleite gegangen, hat das sicher nicht die Kosten reduziert. Im Gegenteil, das hat die Kosten in die Höhe getrieben. Es wäre in solchen Fällen viel besser, jemanden zu nehmen, der die Kosten von Anfang an seriös abgeschätzt hat.
Gerade bei Freiformen, also bei komplexeren Bauaufgaben, ist das aus meiner Sicht ein großes Problem in den aktuellen Leistungsphasen. Ich würde absolut dafür plädieren, dass eine zusätzliche Leistungsphase eingebaut wird, die eine Mockup-Phase ist, die vor der Ausschreibung stattfindet, wo auch der Architekt bzw. die Architektin selber noch im Entwurf ist und wo auch sein bzw. ihr Wissen mit dem Wissen des Unternehmers in das Projekt miteinfließen kann.
GAM: Das Mockup als Schlüssel, sehr interessant! Mir fällt dazu die Anekdote ein, die mir Peter Cook zur Entstehung des Grazer Kunsthauses erzählt hat. Das 1:1 Mockup der Fassade, das sie damals gebaut und auf der Biennale in Venedig gezeigt haben, hat für die Realisierung ebenfalls eine Schlüsselrolle gespielt …
KS: Man versucht oft, sich das Mockup zu ersparen, aber das ist genau der falsche Ansatz! Für ArchitektInnen ist es das erste Mal, dass sie praktisch, physisch erleben, was sie entwerfen. Das ist ein unglaublich schöner Moment, nicht nur für die ArchitektInnen, auch für die Bauherrschaft, weil sie das erste Mal spüren, was sie bekommen werden. Eine zweite Erfahrung, die wir gemacht haben, ist, dass Mockups die Entscheidungsprozesse beschleunigen, weil Fragen fundierter geklärt werden können. Damit spart man am Ende sogar Zeit.
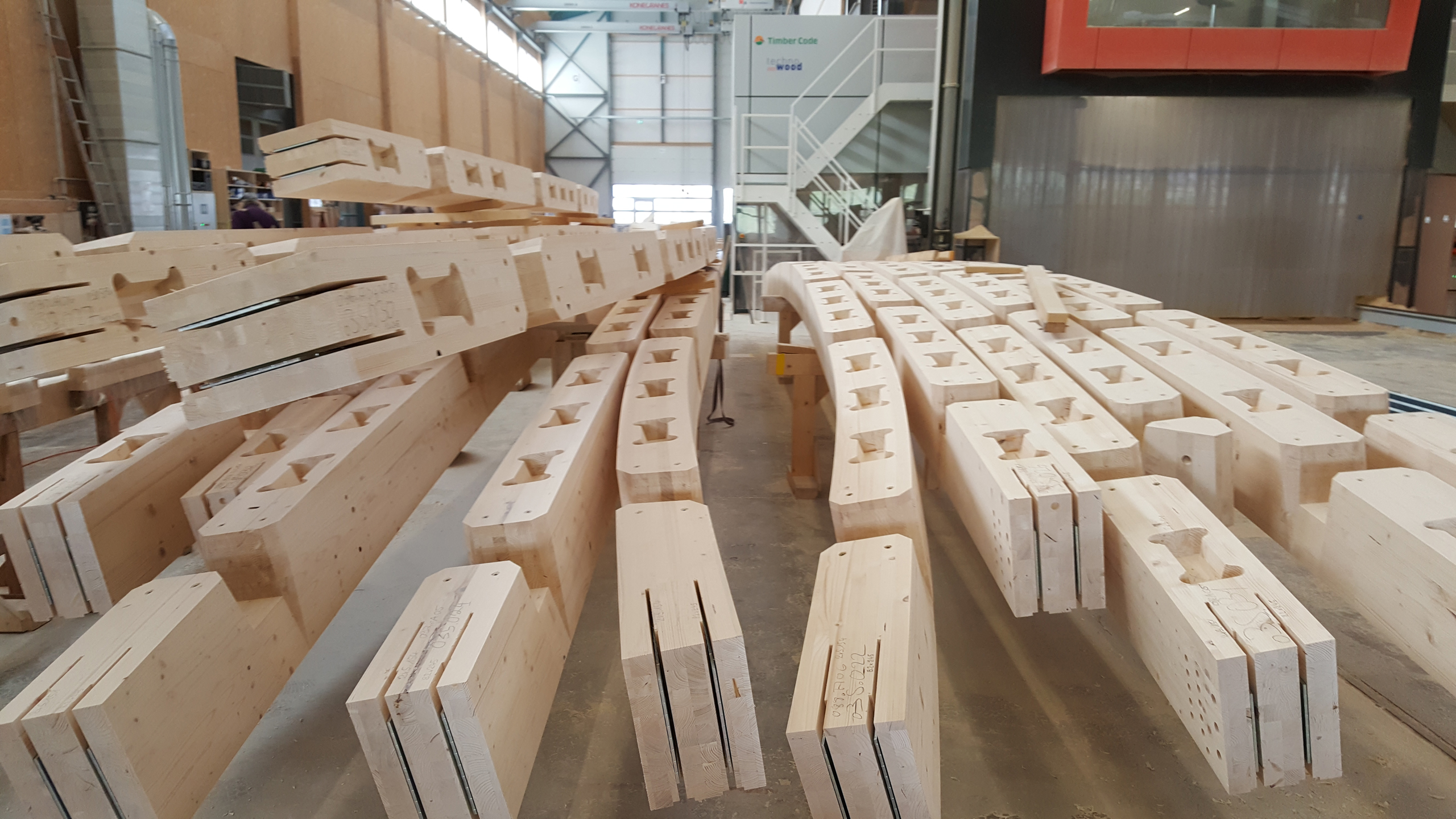
© Blumer-Lehmann AG
GAM: Bei manchen Architekturbüros, mit denen ihr öfter zusammenarbeitet, müsst ihr diesbezüglich wohl keine Überzeugungsarbeit leisten. Mit Shigeru Ban beispielsweise habt ihr ja schon eine ganze Reihe an Projekten gemacht. Ich nehme an, dass Mockups da eine wichtige Rolle spielen. Wie läuft die Zusammenarbeit mit dem Büro Shigeru Ban?
KS: Wir haben nicht nur Projekte mit Shigeru Ban gemacht, sondern auch sehr viele mit Norman Foster. Diese Büros kommen sehr früh in der Entwicklung ihrer Projekte auf uns zu und machen dann meistens nicht nur ein Mockup, wenn der Entwurf mehr oder weniger fertig ist. Nein, diese Büros kommen früh, um zu testen, was mit Holz möglich ist, wie weit sie gehen können, um ihre Architektur damit umzusetzen. Da stehen auch die Bauherren dahinter, dass die Mockups gemacht werden, bis der Entwurf fix ist und auch die technologischen Möglichkeiten detailliert abgeklärt sind. Oft probieren wir mit diesen Büros neue Technologien aus.
GAM: Das gilt eindeutig auch für das neue Swatch Hauptgebäude in Biel, das ihr mit Shigeru Ban entwickelt habt. Das Projekt gehört zu den größten, auch umfangmäßig, die ihr je realisiert habt. Ich denke, es war 2015, als wir euch mit einer Studierendengruppe besucht haben. Da habt ihr uns damals schon ein beeindruckendes Mockup von diesem Swatch Projekt gezeigt. Das Projekt war also schon eine Zeit lang in Vorbereitung. 2019 ist es dann fertig gestellt worden. Was waren bei dem Projekt die größten Herausforderungen? Hast du das Projekt von Anfang an mitbetreut?
KS: Ich habe die Produktion von Anfang an mitbetreut. Ich habe 2015 angefangen und ich glaube im Herbst/Winter 2015 ist der Zuschlag gekommen, dass wir das Projekt bauen können.
GAM: Davor gab es aber schon das Mockup.
KS: Davor war das Mockup. Diese Freiformprojekte haben meistens eine relativ lange Vorlaufzeit. Ich weiß nicht genau, wie viele Jahre schon vergangen waren, bis die Produktion startete. Ich bin in dieses Projekt in dem Moment reingekommen, als die Produktion startete. Es war klar, dass wir das als Blumer-Lehmann nicht alleine stemmen können. Wir haben in einem Verbund mit fünf verschiedenen Holzbaufirmen an diesem Projekt gearbeitet. In Deutschland, in Frankreich und auch in der Schweiz waren Holzbaufirmen beteiligt, um die insgesamt 4.600 Teile fristgerecht zu fertigen. Ein Novum und damit auch eine Herausforderung war, das zu organisieren. Durch die räumliche Distanz konnte man den Aufbau vorher nicht testen. Die Teile sind alle direkt auf die Baustelle gekommen und mussten auf den Millimeter genau passen.
GAM: Wer hat das Ganze dann koordiniert?
KS: Die Fäden sind bei uns zusammengelaufen, aber es war eine Zusammenarbeit von SJB Kempter Fitze AG als Statiker, der Firma Design-to-Production, die die Daten vorbereitet haben und uns, die die Logistik und die ganze Projektplanung, und Organisation sowie das Risiko übernommen haben. Design-to-Production haben unterschiedliche Daten unterschiedlichen Holzbauern geschickt, je nachdem wie deren Produktion eingerichtet war. Wir haben die Daten im Rhino-Format bekommen, also als reine Geometriedaten und haben dann aus diesen Geometriedaten den kompletten Maschinensteuerungscode geschrieben oder programmiert und gescriptet.
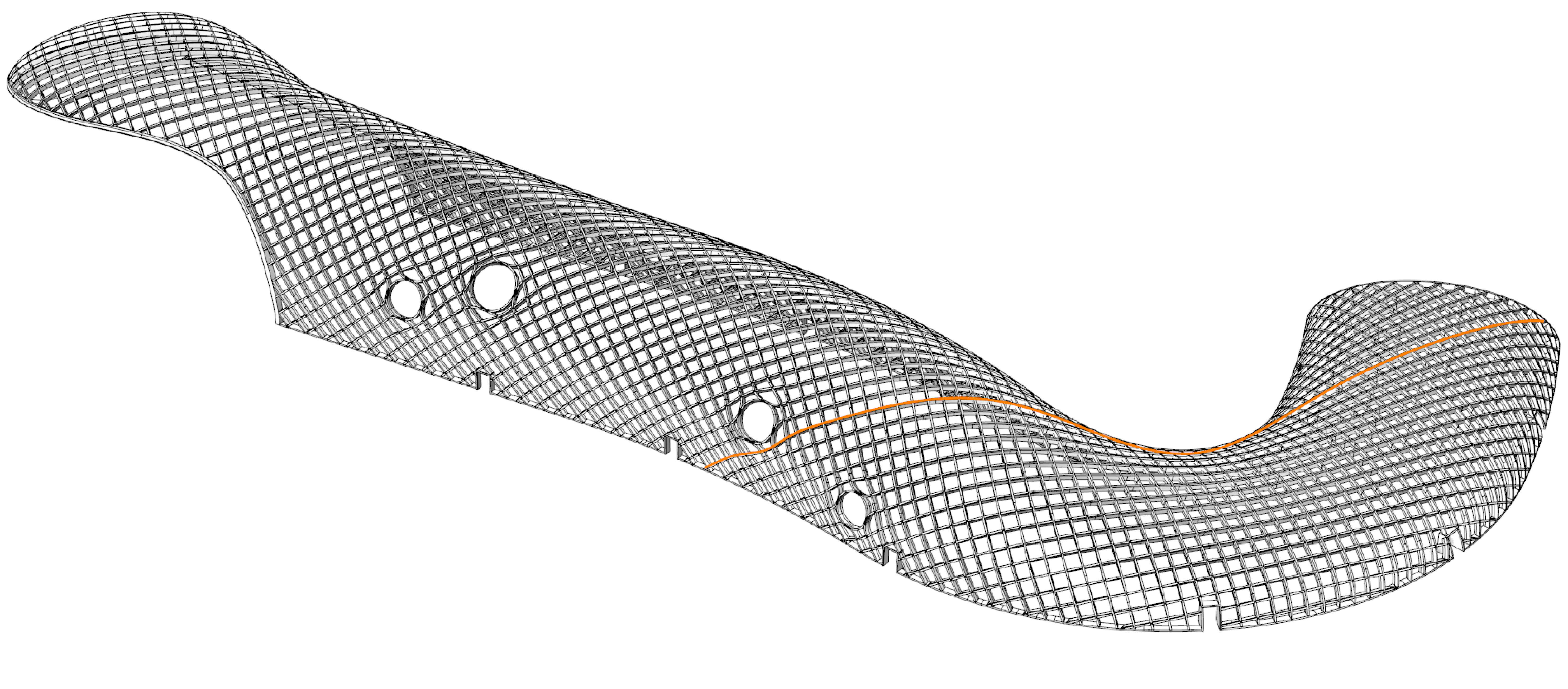
© Blumer-Lehmann AG
Es gab verschiedene Herausforderungen. Eine Herausforderung war der Verbund von den verschiedenen Firmen. Eine andere war die Konstruktion selbst. Im Holzbau unterscheidet man den Stababbund und Platten und Träger. Bei dem Gebäude in Biel ist es so, dass wir lauter gebogene Träger haben. Das sind keine Stäbe und es sind auch keine Platten. Das heißt, die industriellen Prozesse, die es gibt, die Platten zuzuschneiden und zu verarbeiten, funktionieren nicht. Wir mussten für dieses Gebäude diese Prozesse komplett neu entwickeln. Das ist natürlich ein Risiko gewesen.
Ganz entscheidend ist der Faktor Zeit. Wenn wir ein Bauteil berechnen mit einer Zeit X und einen gewissen Puffer haben, dann ist das immer ein Stück weit Spekulation. Es kann sein, dass wir etwas nicht bedacht haben und dieses Bauteil nur in der drei- oder vierfachen Zeit hergestellt werden kann. Wir haben über ein Jahr jeden Tag 24 Stunden ohne Pause gearbeitet. Unsere Fräsmaschinen standen nie still. Wenn wir uns verschätzt hätten, dann hätte das Projekt auch ein, zwei oder drei Jahre länger dauern können. Das ist natürlich eine riesige Herausforderung, eine hohe Kunst, sich da nicht zu verschätzen.
Die Prozesse, das heißt diese verschiedenen Verbindungen im Holz, die wir für das Projekt entwickelt haben, waren völlig neu. Am Anfang hat es ca. 45 Minuten gedauert, bis wir die rausgefräst hatten. Wir haben diese Prozesse im Projekt runterreduzieren können auf drei bis fünf Minuten. Wenn man das hochskaliert, dann sieht man, was für eine Herausforderung es ist, so ein Projekt so zu kalkulieren, dass man es danach auch fristgerecht produzieren kann.
GAM: Dieser Zeitfaktor wird ja leicht unterschätzt. Wir erleben das auch bei unseren 1:1 Projekten, die wir mit Studierenden erstellen. Aber bei einem so gewaltigen Projekt wie dem Swatch Hauptquartier ist man natürlich in einer ganz anderen Dimension.
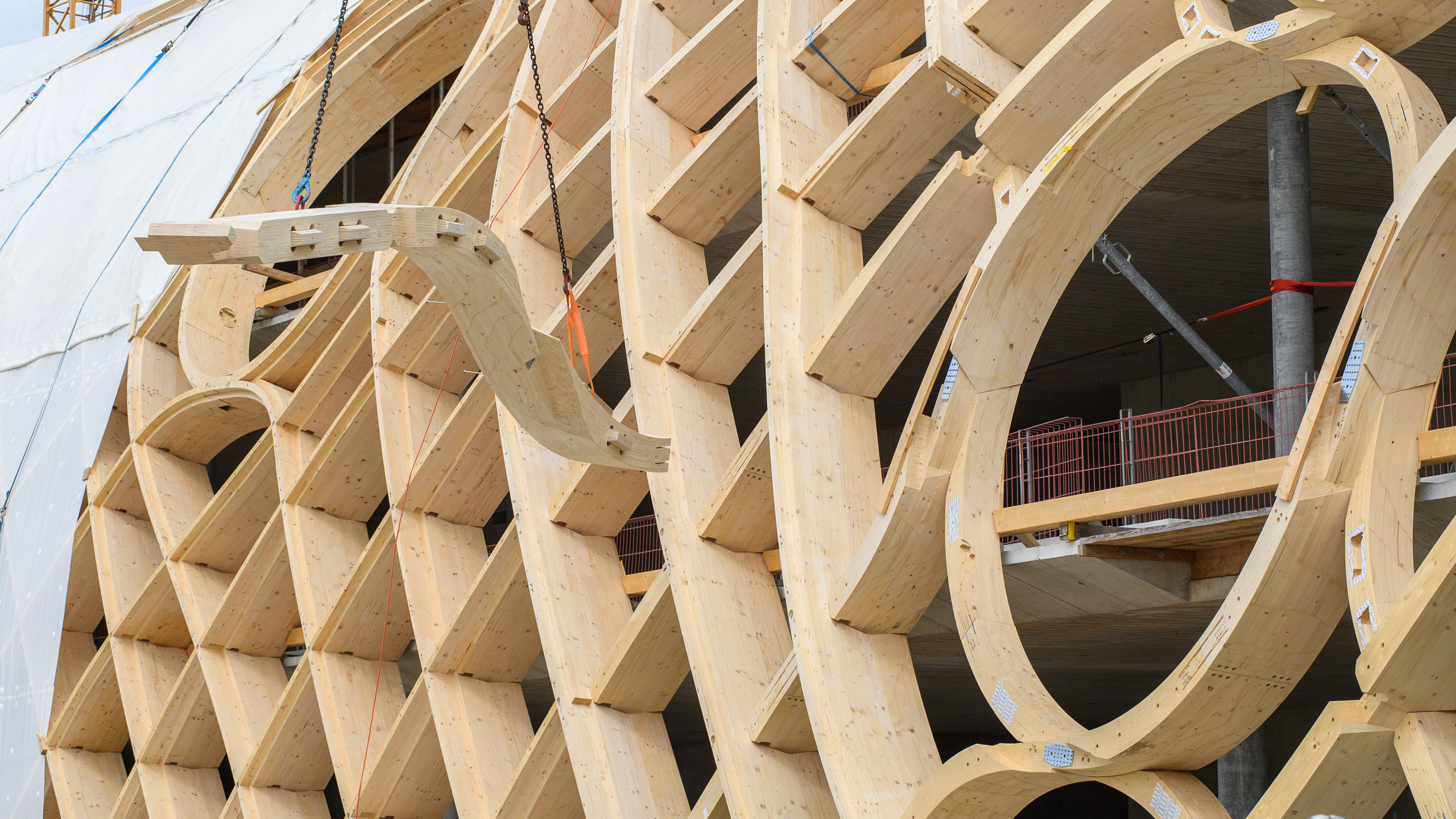
KS: Ganz kurz dazu: Wenn man sich das „Bird’s Nest“ – das Olympiastadion von Herzog & de Meuron in Peking – anschaut, dann hatte das natürlich auch einen strikten Zeitplan. Aber dort konnten sie einfach die Anzahl der Arbeiter auf der Baustelle multiplizieren. Da waren dann Tausende von Arbeitern auf der Baustelle. Bei vielen Architekturprojekten geht das: die kann man beschleunigen, indem man einfach mehr Leute aufbietet. Wir konnten das nicht, denn wir mussten die Sachen auf unserer Maschine fräsen.
GAM: Ihr hättet aber eine zweite Fabrik oder eine dritte noch daneben stellen können und das parallel machen, wenn Geld keine Rolle spielt.
KS: Das geht aber nicht innerhalb des Zeitrahmens. Wenn auf einer Baustelle Leute Fenster montieren, kannst du ohne weiteres 20 Fenstermonteure von einem Tag auf den anderen organisieren, die dir dann helfen, die Baustelle zu beschleunigen. Aber eine Fabrik baust du nicht innerhalb von zwei Wochen. Und die Maschinen, die wir zum Fräsen verwenden, sind ja auch keine Massenprodukte. Die bekommst du nicht in diesem Zeitrahmen gebaut. Deswegen ist der Zeitfaktor in unseren Projekten mit so viel Risiko behaftet. Und Geld spielt immer eine Rolle, denn schließlich sollte jedes unserer Projekte auch betriebswirtschaftlich funktionieren.
GAM: Zurück zu den Besonderheiten der Konstruktion beim Swatch Projekt. Dass Holz ein anisotroper Werkstoff ist, hast du schon erwähnt. Für die doppelt gekrümmten Stäbe, die dann eben keine Stäbe mehr sind, ist das natürlich höchst relevant. Sie sollen ja möglichst in Faserrichtung belastet werden. Kannst du erklären, wie man diese doppelt gekrümmte Faserrichtung beim Swatch-Projekt erreicht hat?
KS: Am einfachsten lässt sich das mithilfe von Bildern erläutern. Auf Abbildung 13 sieht man, dass Holz extrem gute Eigenschaften aufweist, wenn Druck und Zug entlang der Faser wirken. Die Eigenschaften von Druck und Zug werden schlechter, wenn man von dieser Richtung abweicht – bis ca. fünf Grad sind sie noch O.K. Quer zur Faser sind die Eigenschaften extrem schlecht.
GAM: Also bis zu fünf Grad ist gerade noch O.K.?
KS: Ja, das ist noch O.K. Das ist relativ wenig. Das bedeutet, dass man beim Fräsen eines Bauteils genau darauf achten muss, dass der Kräfteverlauf immer entlang dieser Faser geht. Wir sprechen hier vom Faseranschnittswinkel. Auf Abbildung 11 sieht man einen einfach gekrümmten Träger. Theoretisch könnte man den auch aus einem riesigen Stück Holz herausfräsen. Aber die statischen Eigenschaften wären dann ganz schlecht, weil die Kräfte darin nicht entlang der Faser laufen. Die Lösung dafür ist, dass man das Holz in einzelne Bretter schneidet und dann biegt und im gebogenen Zustand verleimt. Für einfach gekrümmte Träger geht das recht effizient, das kann man komplett maschinell machen.
Für doppelt gekrümmte Träger ist das allerdings viel komplizierter (Abb. 12). Man kann ein Brett ja nur in eine Richtung biegen. Deswegen muss man das ganze Verfahren zweimal machen. Wenn der einfach gekrümmte Träger fertig ist, schneidet man ihn in der anderen Richtung in Bretter und krümmt und verleimt ihn in diese zweite Richtung. Da kann man sich vorstellen, wie viel komplizierter es ist, dieses Holz wirklich in die richtige Form zu kriegen. Wenn man die Abbildung genauer betrachtet, sieht man, dass es keine normalen Bretter mehr sind. Das sind gekrümmte Bretter, die hier ein zweites Mal gekrümmt wurden. Die Idee ist immer die gleiche. Man versucht, das Holz so hinzubekommen, dass der Kräfteverlauf der Faser folgt. Wenn ich Holz biege, dann versucht es, sich elastisch wieder zurückzuformen. Das heißt, in dem Moment, wo ich das Holz biege und miteinander verleime, habe ich einen Zustand, der stabil ist. Aber jede dieser Lamellen ist unter Spannung. Das ist also ein ganzes Bauteil, in dem unglaublich viele Spannungen drinstecken.
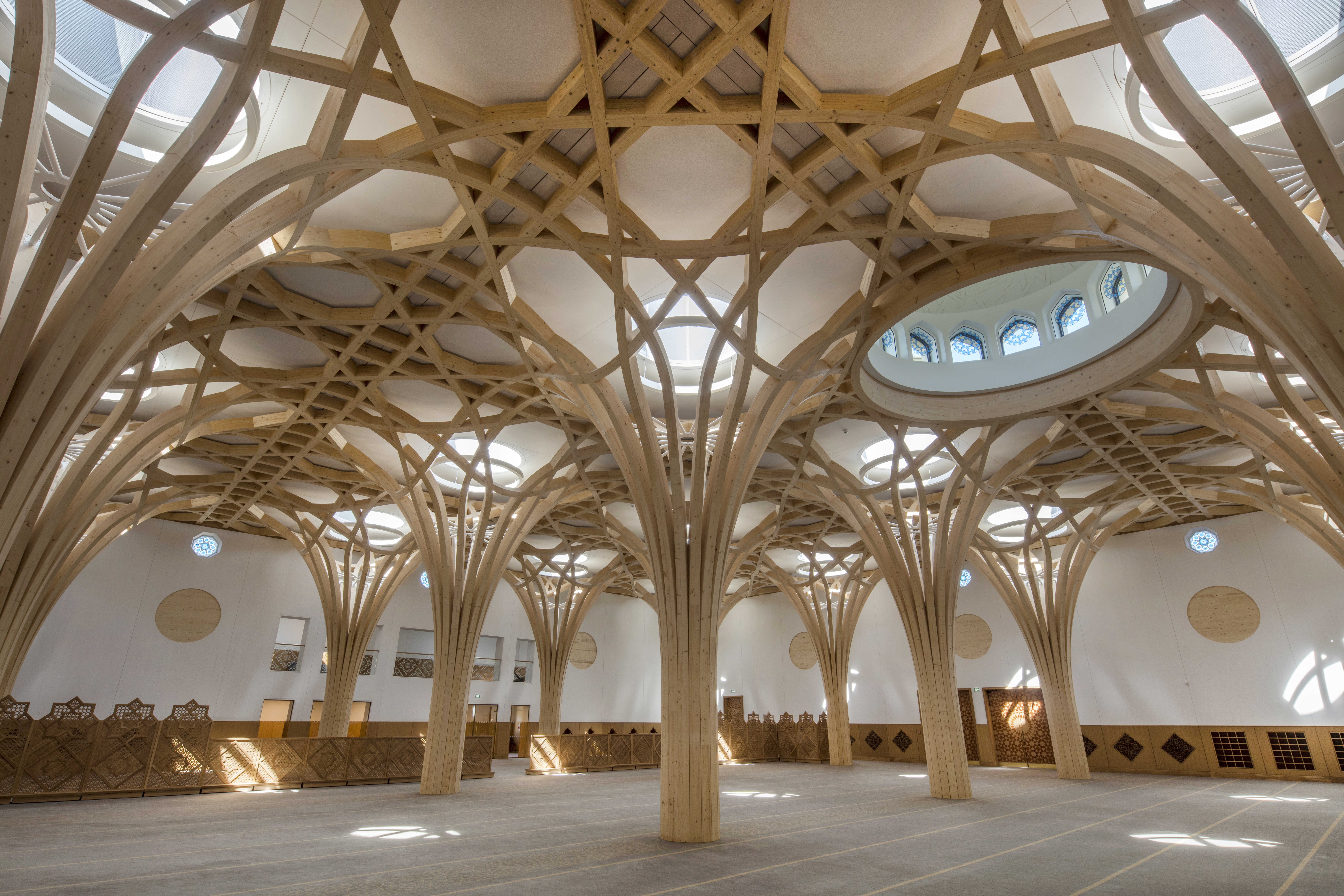
© Morley von Sternberg
GAM: Diese gekrümmten oder doppelt gekrümmten Träger sind dann aber nur die Rohlinge, aus denen dann die endgültigen Träger präzise herausgefräst werden. Sind diese Rohlinge beim Swatch-Projekt auch bei den einzelnen Holzbaufirmen erstellt worden?
KS: Bei Swatch haben wir mit der Firma Hess zusammengearbeitet, die haben das anders gemacht. Das, was ich dir vorher gezeigt habe, war, dass man die Lamellen in eine Richtung krümmt, dann salamimäßig aufschneidet und dann in die andere Richtung krümmt.
GAM: Das „Salamiprinzip“. Daneben gibt es aber auch noch das sogenannte „Spaghettiprinzip“ …
KS: Genau. Die Firma Hess hat nach dem „Spaghettiprinzip“ gearbeitet. Die haben statt Brettern einfach Stäbchen genommen. Die Stäbchen haben die Möglichkeit, dass man sie in beide Richtungen krümmen kann. Die Stäbchen hat man gebündelt in eine Form hineingelegt und verleimt. Dadurch hat man sich einen der beiden Prozesse gespart.
GAM: Und die Firma Hess hat das auch für die anderen Betriebe gemacht?
KS: Genau!
GAM: Dann war sozusagen nur mehr der Feinschliff zu machen?
KS: Ja. Man versucht natürlich so sparsam wie möglich mit dem Material umzugehen. Ideal wäre, wenn man überhaupt nichts mehr abfräsen müsste in der Längsbearbeitung, aber mit dem ganzen Leim schafft man das nicht.
Wir schaffen auch nicht, die Krümmung perfekt hinzubekommen. Auch bei diesen Spaghettiträgern gibt es Rückstellungskräfte, das heißt, das Holz versucht, wieder gerade zu werden. Das ist nicht immer perfekt vorhersehbar. Meistens lassen wir ein Übermaß von zwei Zentimetern bei dieser Löngsbearbeitung und diese zwei Zentimeter fräsen wir ab. Daraus ergibt sich dann noch eine andere Schwierigkeit. Manchmal ergibt es sich, dass ich beim Abfräsen genau auf der Ebene des Übergangs zwischen zwei Lamellen lande. Es kann sogar sein, dass die Schnittebene alle drei Zentimeter vom oberen Stab in den unteren Stab und dann wieder in den oberen Stab wechselt. Das sieht ästhetisch schwierig aus. Deshalb versuchen wir möglichst mit einer Längsbearbeitung innerhalb einer Lamelle oder innerhalb einer Schicht zu bleiben, um auch wirklich die ästhetisch schönen Faserverläufe zu haben. Wenn die einzelnen Stäbe dicker sind, dann ist das leichter, aber das kann man sich nicht immer aussuchen. Auf der Abbildung 14 sieht man, wie dick die Lamellen in Abhängigkeit von der Krümmung sein müssen. Es gibt unterschiedliche Richtwerte, aber meistens sprechen wir von einem Verhältnis von 1:200 von der Lamellendicke zum kleinsten Krümmungsradius im Träger. Wenn ich einen Radius von zwei Metern habe, ergibt das eine Lamellendicke von einem Zentimeter. Brettschichtholzträger haben normalerweise 40 Millimeter starke Lagen. Das lässt sich am günstigsten herstellen. Daraus ergibt sich, dass ein Krümmungsradius von acht Metern ein wirtschaftlich optimaler Radius ist.
Gekrümmtes Holz schlägt sich erheblich auf die Kosten nieder. Wenn ich einen Preis X habe für gerades Holz, dann ist in der Regel ein einfach gekrümmtes Holz zwei bis fünfmal teurer. Bei einer stärkeren Krümmung muss ich dünnere Lamellen nehmen und dann wird das bei den einfach gekrümmten Trägern teurer (Abb. 15). Bei doppelt gekrümmtem Holz wird es sogar bis zu fünfzehnmal teurer. Wir probieren, ein Gebäude so zu segmentieren, dass wir möglichst viel mit einem Krümmungsradius von acht Metern herstellen können, um weniger von dem sehr teuren Holz zu verwenden.
Auf den Abbildungen 9 und 10 sieht man ein Mockup, das wir für die Moschee in Cambridge gebaut haben (Abb. 8). Im unteren Bereich haben wir einfach gekrümmte BSH Träger verwendet, die bis in die Krone reichen. Oben mussten wir doppelt gekrümmte BSH Träger verwenden, bei welchen wir auch einen Wechsel der Lamellenschichtung haben. Dieses Mockup haben wir gemacht, um zu sehen, ob man den Wechsel von der Lamellenrichtung oder vom Holz von einem zum anderen sieht. Wenn man genau hinschaut, dann sieht man das natürlich, aber es funktioniert trotzdem.
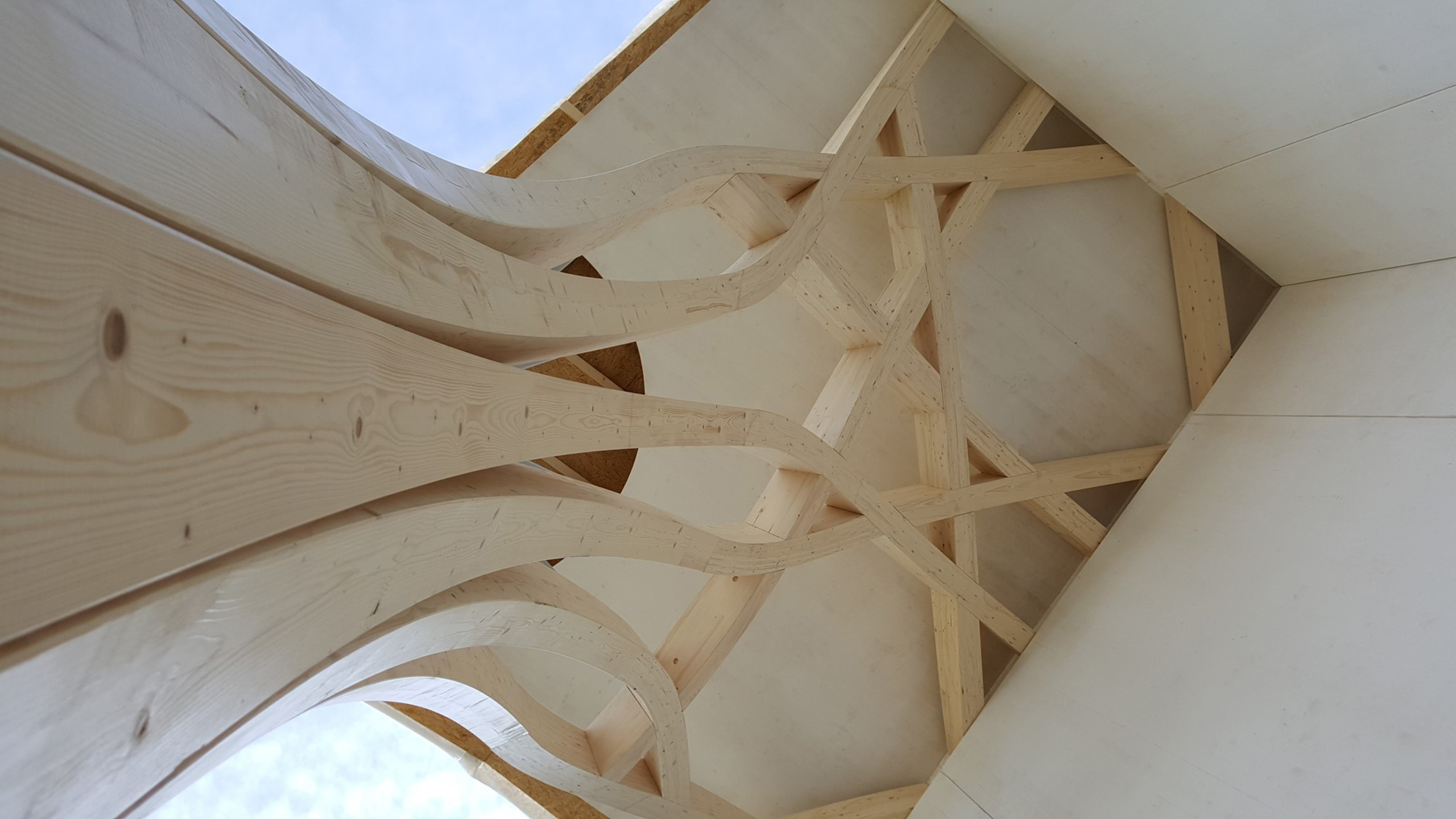
© Blumer-Lehmann AG
GAM: Das heißt, es ist eine Optimierungsaufgabe, bei der auch die Ästhetik immer mit hineinspielt. Es ist ja schöner, die dickeren Querschnitte zu haben, rein optisch. Je dünner die „Spaghetti“ werden, desto mehr entfernt man sich auch von dem, was man von der Anmutung her mit Holz verbindet. Letztlich geht es ja fast wieder in die Richtung einer Faserplatte, auch wenn die Faserrichtung noch stimmt. Das ist alles wirklich sehr beeindruckend und spannend auch als Optimierungsaufgabe. Aber angesichts dieses enormen Aufwands stellt man sich doch die Frage, ob das noch verhältnismäßig ist. Wäre so eine Struktur mit einem homogeneren Baustoff, zum Beispiel in Stahl, nicht einfacher und letztlich vielleicht auch materialgerechter herzustellen?
KS: Bei der Moschee haben wir zum Schluss relativ dünne und elegante Träger hinbekommen. Das heißt, wir schaffen es wirklich, mit der Faser zu arbeiten und die Faser so zu aktivieren, dass wir das Holz optimal in den Bauwerken anwenden können. Diese Freiformen sind Leuchtturmprojekte. Bei diesen Projekten geht es nicht darum, ein möglichst günstiges Projekt herzustellen. Leuchtturmprojekte braucht jede Gesellschaft, jedes Land, jede Stadt braucht seine kleinen Leuchtturmprojekte. Keine Stadt in Europa möchte einfach nur banale 08/15 Architektur haben. Wir brauchen das für den Tourismus, wir brauchen das für das Selbstbewusstsein und für die Identität der Städte. Ich glaube, das ist eine zentrale Aufgabe von Architektur.
Was wir mit Holz heutzutage machen, ist die Speerspitze, die zeigt, was mit Holz machbar ist. Es geht nicht darum, einfach nur billig mit Holz zu bauen, Holz zu verwenden, weil es ein billigerer Baustoff ist. Es geht darum, Holz zu verwenden, weil es ein besserer Baustoff ist.
GAM: Bei der Moschee in Cambridge sprecht ihr in Bezug auf die Tragstruktur von Bäumen. Und das ist auch wirklich eine schöne Analogie. Dennoch liegt eine gewisse Absurdität darin, dass in der industriellen Holzproduktion erst mal alle gekrümmten Teile aussortiert werden. Die Bäume, die nicht gerade wachsen, die kann man da nicht brauchen. Und dann macht ihr, aus all diesen geraden Teilen, nach zahlreichen, logistisch komplexen High-Tech-Bearbeitungsschritten wieder etwas, das elegant und mehrfach gekrümmt ist und uns an die Form eines natürlich gewachsenen Baumes erinnert. Wäre es nicht eleganter, wenn man von Anfang an natürlich gewachsene, krumme Teile nehmen würde?
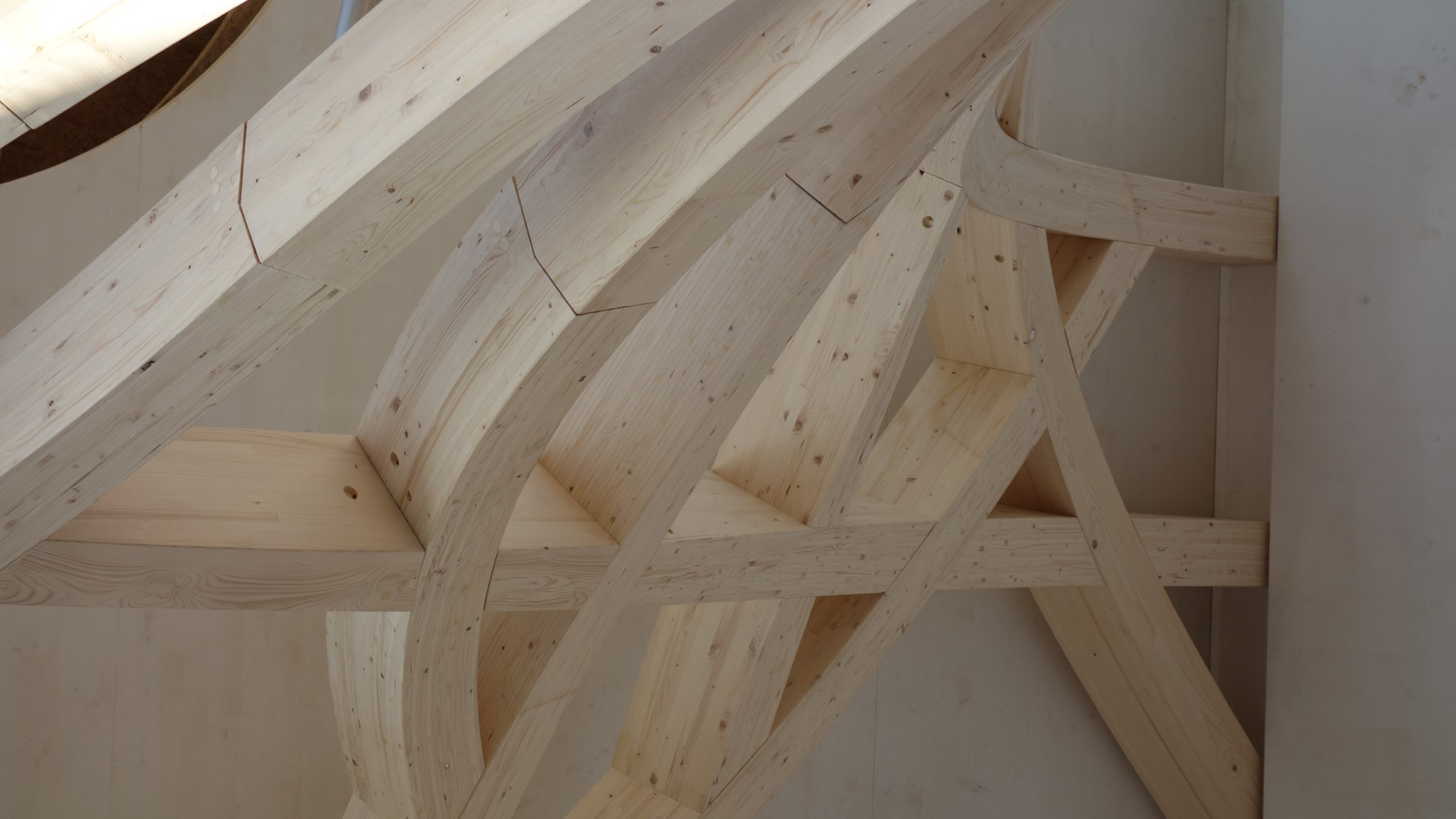
© Blumer-Lehmann AG
KS: Du hast in einem unserer Vorgespräche die Analogie mit der Geige gebracht. Bei der Geige geht es um eine enorme Veredelung vom Holz selbst. Man geht in einen Wald, man sucht sich genau den Baum aus, den man haben möchte für seine Geige, man lässt das Holz jahrelang trocknen, damit man möglichst alle Spannungsrisse herausbekommt, um dann schließlich daraus eine Geige zu bauen, als höchsten Schritt der Veredelung. Diese Geige ist in keiner Weise zu vergleichen mit einer Plastikgeige, die man im Supermarkt kauft. Da sind Welten dazwischen. Es geht da um den Respekt vor dem Material. Diesen Respekt würde ich auch für unsere Arbeit reklamieren. In meinen Augen liegt bei unserer Arbeit der Respekt vor dem Material darin, wie wir mit der Faser umgehen. Für mich ist das ein riesiger Unterschied, ob ich die Faser aktiviere, oder ob ich die Faser nicht aktiviere.
Es ist natürlich auch eine Frage der Perspektive. Wenn meine Perspektive ist, dass man Holz möglichst so, wie es aus dem Wald kommt, also ohne fremde Stoffe, ohne Leim usw. verwenden sollte, dann kommt man zu einer anderen Architektur. Da kommt man aber auch nicht unbedingt zu einer Geige. Aber ich will das eine nicht gegen das andere stellen. Es gibt den Stababbund, Hochhäuser aus CLT (Cross-Laminated Timber), den Modulbau, den normalen Holzbau und die Freiform. Holz ist vielfältig, es ermöglicht viele Ansätze und es geht nicht darum zu sagen, der eine Ansatz ist der richtige und der andere ist falsch. Sondern es geht darum, dass das Material vielseitig nutzbar ist. Es ist genauso in Ordnung, eine Cambridge Moschee mit gebogenen Trägern zu bauen, wo diese Technologie ausgelotet wird, wie es in Ordnung ist, ein Haus mit Mondholz zu bauen, das nur in bestimmten Momenten geschlagen wird und wo für die Verbindungen nur Holznägel verwendet werden. Zum Beispiel beim CLT, da baut man jetzt Hochhäuser. Es gibt Entwürfe, die bis zu 300 Meter hoch sind. Die Frage ist für mich nicht: „Macht es Sinn, 300 Meter hoch in Holz zu bauen?“ Ausprobieren, wieviel geht, was möglich ist, das ist etwas sehr Menschliches. Dass diese Speerspitzenprojekte realisiert werden, dass jemand ein bisschen höher baut als jemand anderes, das gehört in der Welt der Architektur einfach dazu.
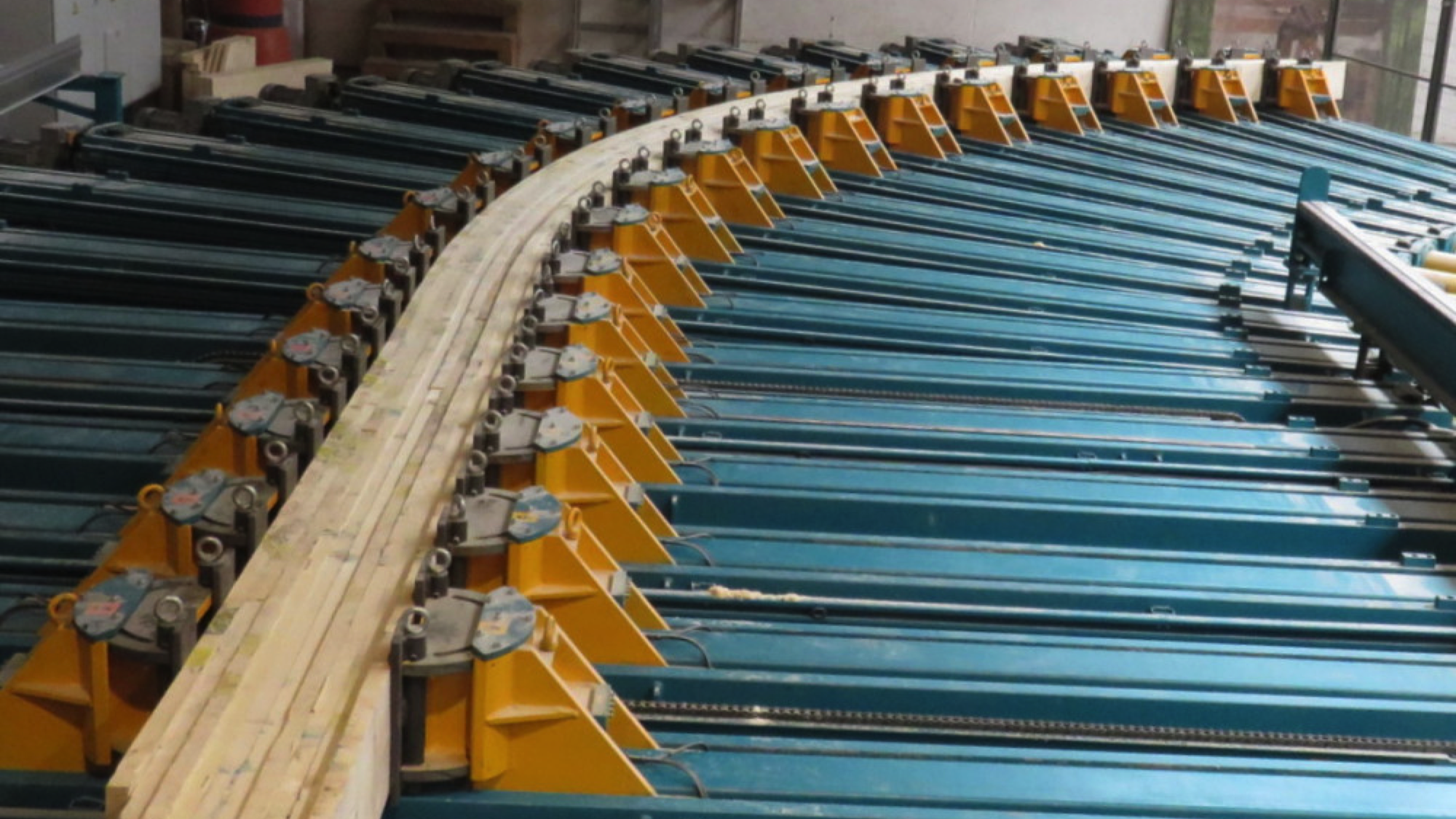
© Blumer-Lehmann AG
GAM: Wie weit haben diese Speerspitzen, wie Du sie nennst, das Potenzial irgendwann im Mainstream zu landen? Im Bereich der IT finden wir das normal, dass wir alle in unseren Taschen Geräte tragen, die vor wenigen Jahrzehnten noch Supercomputer gewesen wären. Glaubst Du, dass in der Holzarchitektur etwas Ähnliches passieren könnte? Werden die Leute sich irgendwann mal aus doppelt gekrümmten und gefrästen Hölzern gebaute Gazebos in ihren Garten stellen, die sie im Baumarkt gekauft haben? Oder glaubst du, dass in diesem Bereich so etwas nicht stattfinden kann?
KS: Ich glaube, dass es Nischenprojekte und spezielle Projekte und Aufgaben bleiben werden. Wenn ich jetzt nur den normalen Wohnungsbau betrachte, wo kann ich denn die Freiform einsetzen? Im Fußboden kann ich sie nicht einsetzen, in der Wand ist es meistens unpraktisch und die meisten Freiformprojekte, die wir haben, ob das Swatch oder die Moschee sind, sind Kuppelbauten und komplexe Dachkonstruktionen. Wir haben eine Villa in der Türkei für Norman Foster gebaut, in der wir auch ein Dach mit einer fliegenden Geometrie über einem relativ rechtwinkeligen Grundriss gebaut haben.
Wie gesagt, ich glaube diese Projekte werden zum größten Teil wirklich Leuchtturmprojekte bleiben. Es kann aber sein, dass es zunehmend auch kleinere Leuchtturmprojekte geben wird. Wir haben jetzt für das Kulturhaus in Böttstein ein Kuppeldach für den Gemeindesaal realisiert und das ist eine relativ günstige Freiform (Abb. 16). Bei diesem Projekt haben wir auch ohne Mockup gearbeitet. Es ist ein Tonnendach, wobei die Konstruktion einem Zollingerdach ähnelt. Das sieht jetzt allerdings nur aus wie ein Geflecht, in Wirklichkeit laufen die Träger nur in einer Richtung bis zum First. In der anderen haben wir kleine Träger, die einfach nur dazwischen gehängt sind. Man musste nur zwei Teile programmieren und diese dann in einer größeren Stückzahl herstellen.
GAM: Wie ist in diesem Fall die Zusammenarbeit mit den Architekten gewesen? Kannst Du Dich da in den Entwurf einbringen? Kannst Du das kurz beschreiben?
KS: Das kann ich nicht beschreiben, weil ich da nicht involviert war. Bei Herzog & de Meuron hatte ich 10 Jahre wirklich in den ersten Entwurfsphasen gearbeitet und jetzt bin ich sozusagen in der allerletzten Entwurfsphase dabei. Ich bin nur dann integriert, wenn es ganz am Anfang vom Entwurf darum geht, ob man etwas dieser Art technisch überhaupt herstellen kann. Also bei der Frage: Kriegen wir die Sachen gefräst?
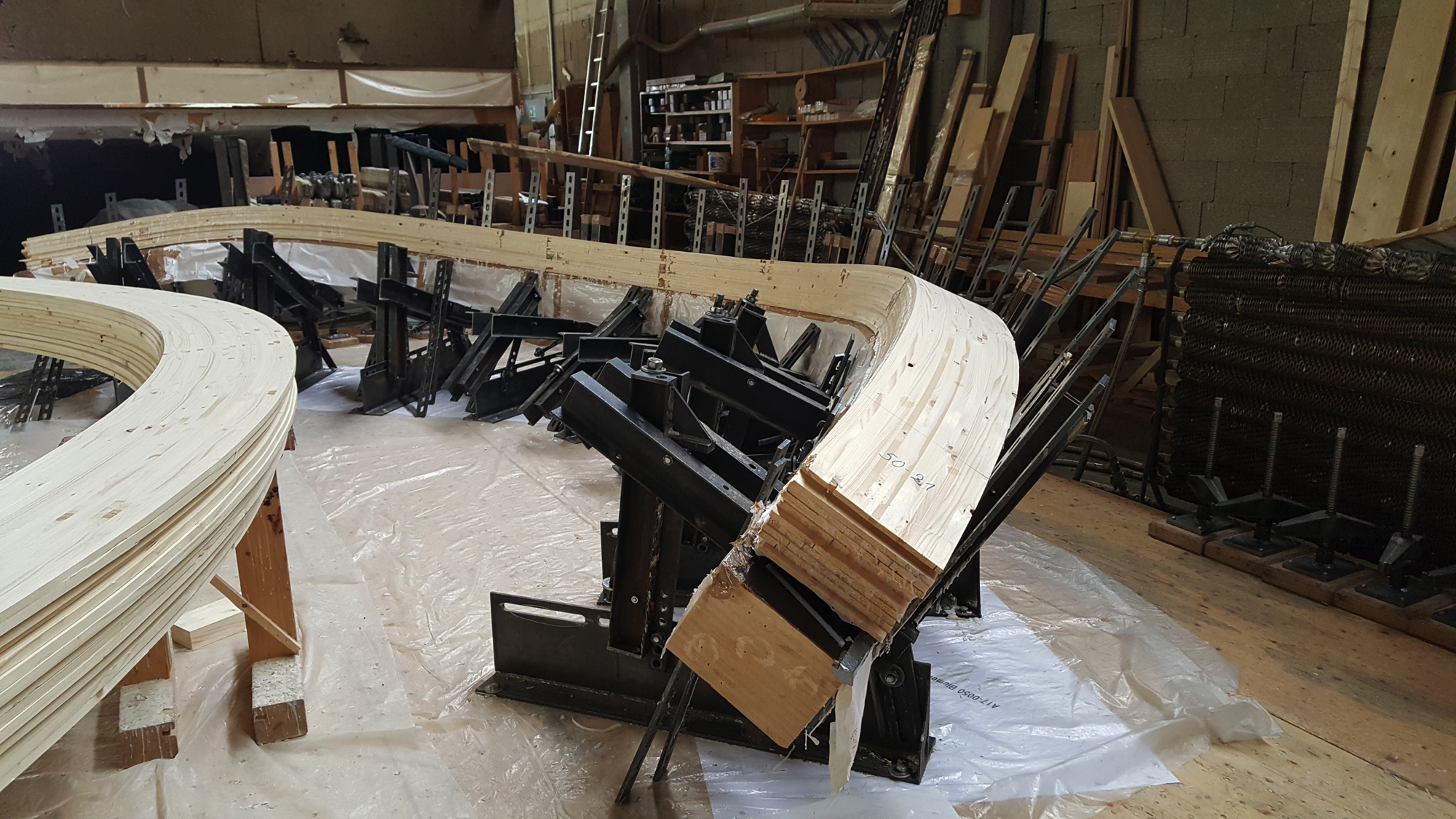
© Blumer-Lehmann AG
GAM: Fehlt Dir das, bei der Konzeptfindung dabei zu sein?
KS: Nein, nicht unbedingt. Es gibt manchmal einen sehr großen Leidensweg bei ArchitektInnen, bis man ein Projekt wirklich auf den Weg bringt. Auch bei Herzog & de Meuron gab es Projekte, die haben viele Jahre gedauert, bis man wirklich in die Realisierung, in die Bauphase gekommen ist. Jetzt bekomme ich Projekte auf den Tisch, die unter einem enormen Kosten und Zeitdruck stehen, aber die sind dann auch nach ein paar Monaten wieder weg. Dann kommen wieder neue Projekte. Ich glaube die Zeit, die ich jetzt habe, ist stressiger, aber spannender. Es ist eine enorme Befriedigung zu sehen, wenn unsere Arbeit das Werk verlässt. Wenn man weiß, da gehen jetzt 60 Lkws nach England. Wenn man diese riesigen Teile auf der Autobahn sieht und man weiß, die gehen nach Rotterdam, nach Korea oder woanders hin. Das ist für mich nach wie vor ein unglaublich faszinierender Moment.
Vor vielen Jahren bei Herzog & de Meuron habe ich mich einmal mit Pierre de Meuron darüber unterhalten, wo ich eigentlich hin möchte in meinem Leben mit der Architektur. Ich habe gesagt, ich sehe drei Bereiche: Den Bereich Design vom Architekten, den Entwurf; ich sehe den Bereich der Akademie, der Ausbildung und diesen Bereich der Produktion. Mich hat im Architekturbüro eigentlich gestört, dass ich in die Produktion nie hineinschauen konnte. Da war es für mich ein logischer Schritt, mal aus dem Büro hinaus und in die Produktion zu gehen. Ich hatte das Glück, zum richtigen Zeitpunkt bei Blumer Lehmann anzukommen, als gerade diese Projekte in der heißen Phase waren. Das war für mich ein sehr spannender Moment.
GAM: Kommen wir nochmals etwas allgemeiner auf die Zukunft des Holzbaus zu sprechen. Du hast ja eingangs schon gesagt, dass das Bauen mit Holz derzeit eine Blüte erlebt, vergleichbar damit, wie Anfang des 20. Jahrhunderts in der klassischen Moderne das Bauen mit Stahl und Glas entdeckt wurde. Wie wird sich das längerfristig entwickeln? Wie lang wird dieser Boom aus deiner Sicht noch anhalten?
KS: Ich glaube leider und Gott sei Dank lange. Leider, weil Holz wirklich ein adäquates Material ist, in der heutigen Zeit mit der Klimakrise, in die wir gerade hineinrutschen oder schon drin sind. Diese Klimakrise ist kein Hype, das ist kein Trend, der in zehn oder fünfzehn Jahren zu Ende gehen wird. Sondern das ist eine neue Realität, mit der wir uns in Zukunft auseinandersetzen müssen.
Gott sei Dank ist Holz ein gutes Material. Es ist nicht nur in der Lage, CO2 zu binden, es hat auch sehr viele bautechnische Möglichkeiten. Deswegen glaube ich und wir bei Blumer Lehmann fest daran, dass das Bauen mit Holz jetzt nicht nur ein zeitlich kurzer Trend, ein Hype ist, dem man nachgeht und den man dann wieder verlässt. Ich glaube, dass das Material in der Architektur schon jetzt eine große Rolle spielt, und in Zukunft noch eine größere Rolle spielen wird.
GAM: Was empfiehlst Du ArchitektInnen in Bezug auf das Bauen mit Holz?
KS: Ich würde jungen Architektinnen und Architekten empfehlen, in ihrer Ausbildung einen Holzbauer zu besuchen oder noch besser ein Praktikum bei einem Holzbauer zu machen. Ich glaube, wenn ich mein Studium nochmals wiederholen könnte, hätte ich wahrscheinlich kein Praktikum in Architekturbüros gemacht, sondern bei einem Holzbauer. Ich glaube, das ist für einen jungen Architekten bzw. eine junge Architektin eine unglaubliche wertvolle Erfahrung.
GAM: Vielen Dank für das Gespräch!